Extending the operational life – protecting and improving our sensor functions,
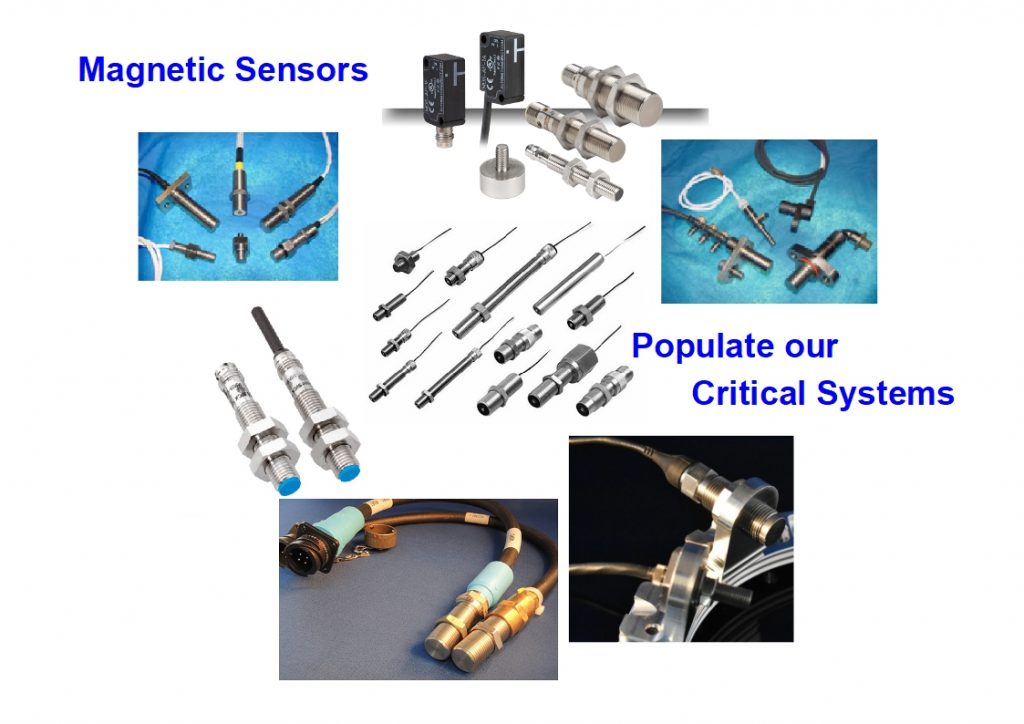
Inductive & magnetic sensors rely on their magnetic field gradient being interrupted or distorted, thus inducing a signal / imposing a hall effect change to the flux gradient.
These sensors rely on accurate positioning and consistent signal recognition,
Because these sensors have a Magnetic field emanating from their signal generator, this part of the probe/sensor can become coated with and influenced by the ferrous/ferromagnetic debris, circulating within the fluids, that is attracted to it.
This can then corrupt the validity of the sensor, and result in inaccurate signal recognition (position) and timing, even during early stages of use.
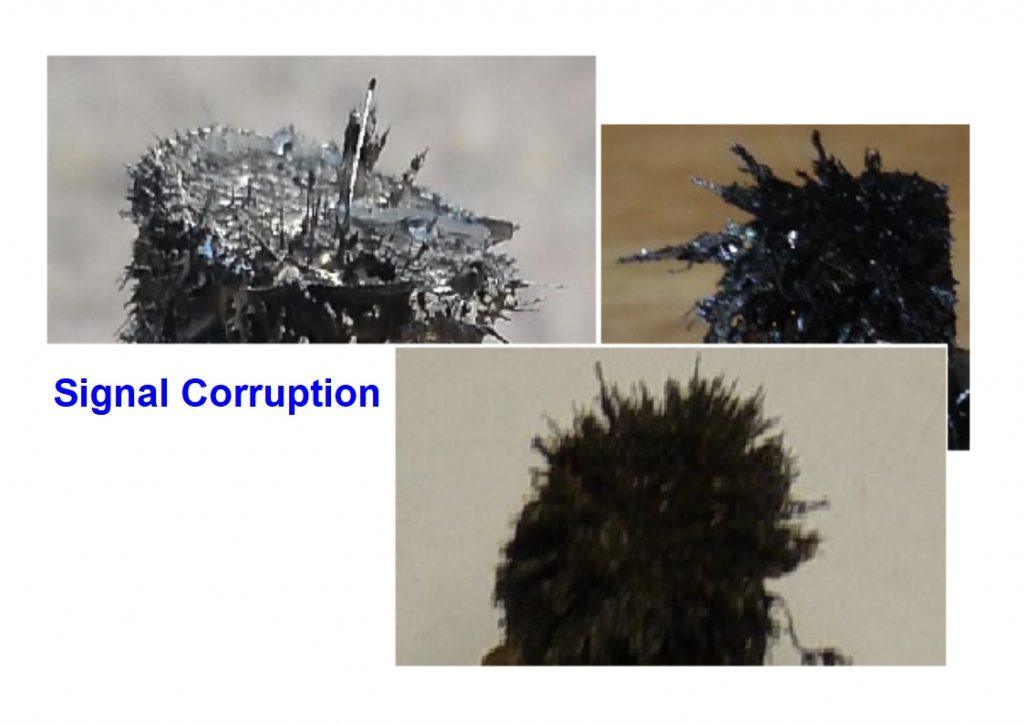
In systems that are immersed in fluids, such as hydraulics, transmissions, etc… these systems contain ferrous debris in significant quantities, typically present in three distinct stages :-
- Despite cleaning during production, contamination is frequently built into the components and the system ‘During Manufacture’.
- During Break-in (Running In) high levels of contamination is present, as the components/systems contact surfaces bed into each-other.
- During normal system use, wear and tear takes place, generating microfine ferrous contamination.
It is very difficult for conventional filtration, i.e. barrier/media filtration cartridges to address this problematic contamination and effectively remove this fine ferrous particulate from fluids,
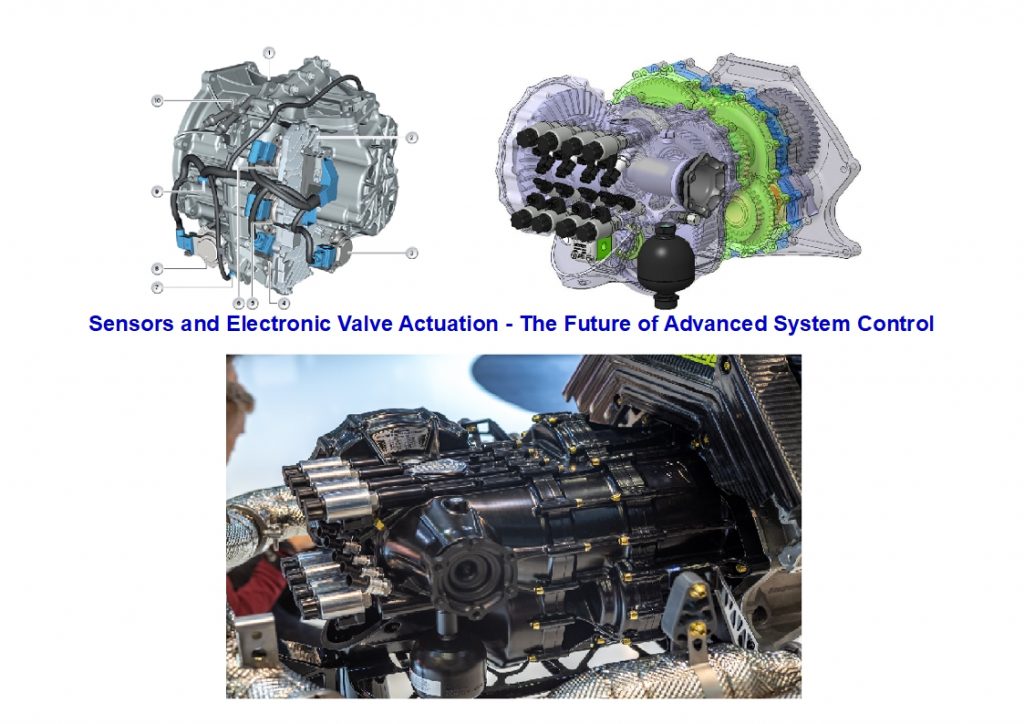
Explantation…
In mechanical systems, the ferrous contamination is typically very small in size (typically sub 10 micron), this is because it is generally generated from hardened… bearing & contact surfaces throughout our systems, subsequently these surfaces do not shed their material easily,
The ferrous is thus torn from these surfaces in tiny particles, which are not only small, but super hard and super sharp.
Conventional filtration is rated by pore size, so any particulate smaller that the pore size simply passes through the filter media (imagine a sieve screening out say husk from flower etc).
It is possible to produce microfine conventional filtration,
But it would be so restrictive to fluid flow, very costly and so large in size, (to provide sufficient surface area for fluid flow), that it is a non viable proposition from a space-claim, high purchase cost and function perspective, to be a viability for our fluid systems,
So a compromise is struck for/with all of these factors.
Being typically smaller than the pore size of conventional filters, these ferrous particles can recirculate through them, and thus causing not only further system & component wear and further contamination generation, but the contaminating of our sensors blinding/corruption of our system sensor signals, and thus incorrect system function and indeed failure.
Just such a simple issue with a sensor, can at best dramatically affect system functionality or indeed stop the whole system.
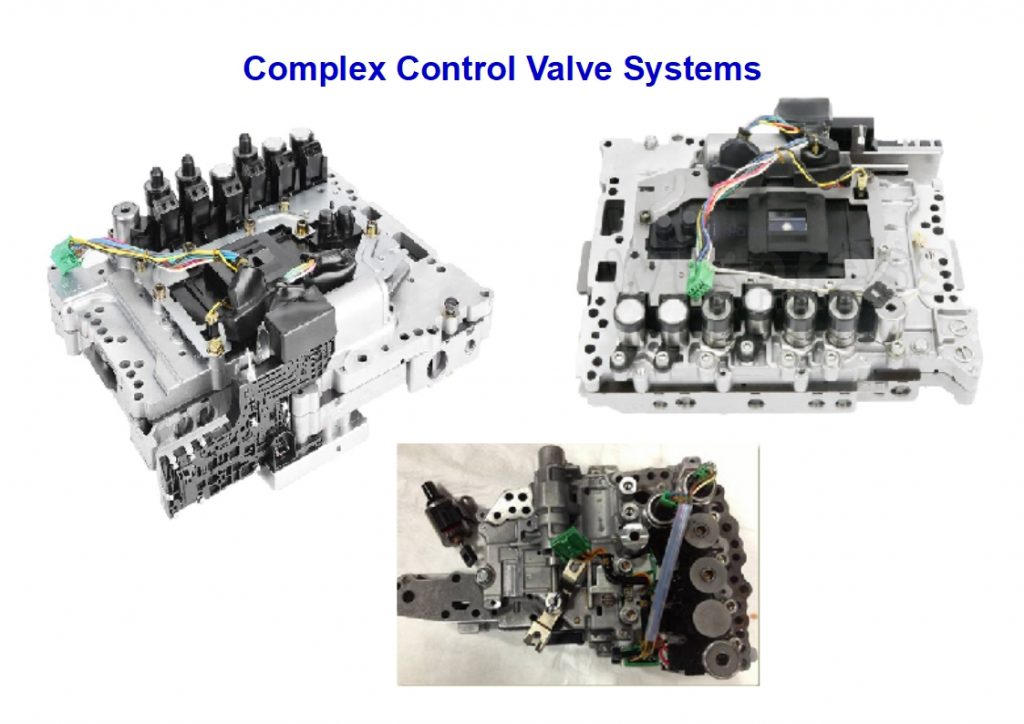
This is hardly surprising…
When you consider that 80% + of the systems/products we produce globally are made from Steel & Iron!
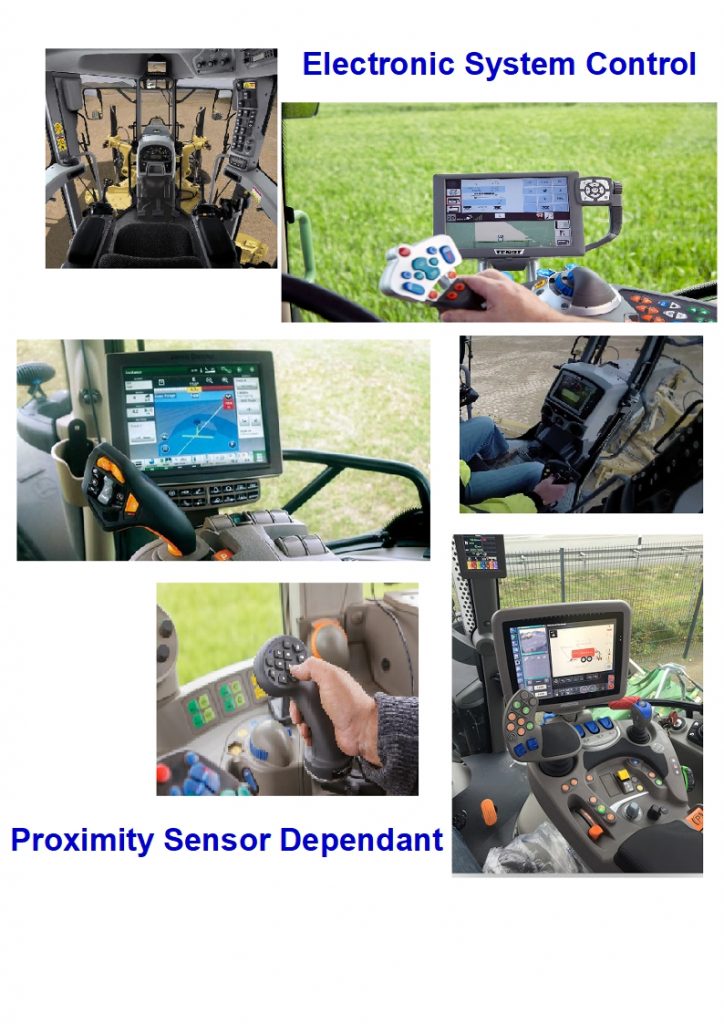
Solution :-
Fortunately a solution is possible, and readily available.
Since the main protagonist in this problem is ferromagnetic, it makes complete sense to use magnetics to solve the issue,
But a magnet alone will not resolve our issues, as the humble magnetic drain plugs fitted to most systems demonstrates.
As these magnetic plugs are just a random attempt to address the performance shortfall of conventional filters (otherwise why fit them in the first place), but they clearly demonstrate that our industry recognises the existence of the conventional filter issues, and has done for decades,
There has just not been a technology available to resolve these issues once and for all… systematically.
Until Now!
A technology developed from the high performance racing industry, and used in Formula 1 since 2007, is now being adopted and used by Major OEM’s worldwide, is available to the mass market, and is clearly demonstrated to resolve numerous issues caused by contamination left in circulation by conventional filtration, and experienced in & by our systems.
Described by its designer as “ Just a very novel was to filter fluids and gasses using clever magnetic flux gradients”
Its called ‘Magnom’ (Magnetic Oil Module), and is tested and demonstrated to remove the microfine ferrous in our systems up-to 100% efficiently, single pass… and does not discriminate by particle size, be it 1 micron or 1 mm + in size.
It is non restrictive to fluid flow, even when full of collected contaminants, and is Bi-Directional,
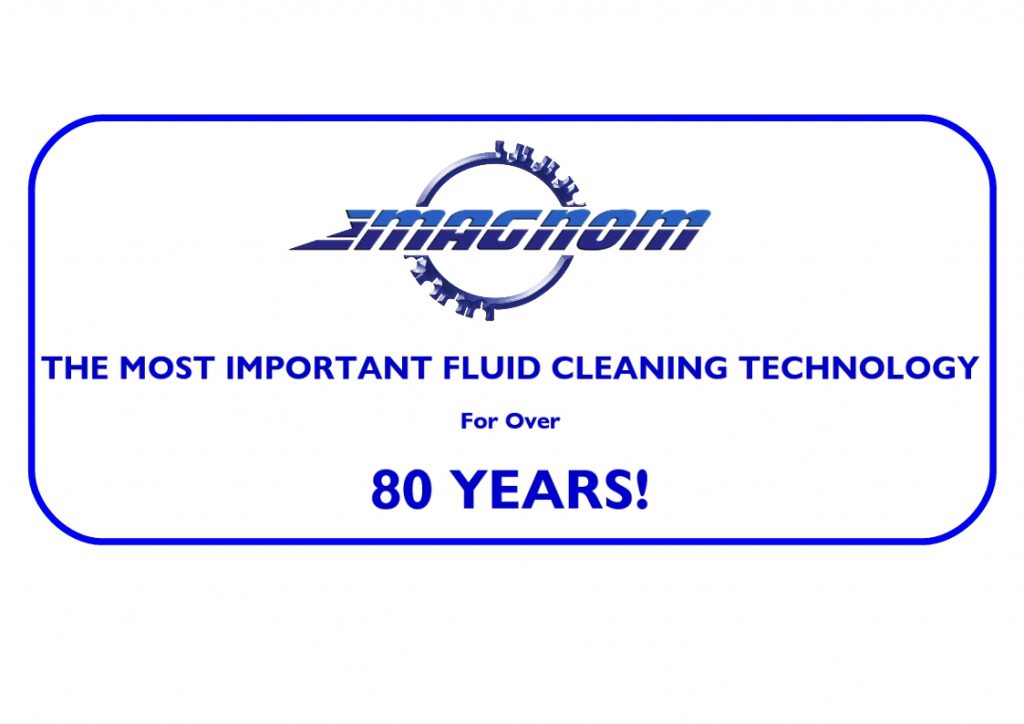
Which means…
For the first time, efficient and effective filtration can be employed on the suction side of a Pump, and also in the bi-directional circuit of a hydrostatic system, almost anywhere in the system, where protection is required, and value can be delivered for the user.
Thus removing the damaging and problematic contamination, that causes problems with our system sensors, as well as the other related damage this highly aggressive particulate causes.
As we become more reliant on sensors, and employ more and more of them in our electronically controlled systems, this becomes a growing issue for us all.
The reliability issues caused by the sensors own magnets harvesting ferrous particulates in the fluid/systems become a greater issue for us, so its fortunate a low cost solution is available to us.
As is often the case… what is adopted in the extrema environments like Formula 1 today, becomes employed in our everyday products tomorrow.
Solenoidal pilot valves…
As we move to remote control (typically joy stick) then we are also more reliant on solenoidal pilot valves.
Particularly in Hydraulic systems, it will be clear to most engineers that :-
These electrical pilot valves, do not have the power of the hydraulically actuated pilot valve, so the very same hard metallic particulate can easily jam these valves, as they have considerably less sheer power of their hydraulic cousins.
Used in conjunction with and dependant of the proximity sensors, the use of this new magnetic technology can deliver benefits for both components, as well as the system as a whole.
Why remove some contamination to a particle size?
When you can remove all of the most aggressive and damaging contaminant, irrespective of its size?
Not just bi-directional & non restrictive… Magnom technology can also hold approximately 40 X more contamination than conventional filters… ‘size for size’.