Cleaning general Service & Production water.
It is important that cooling systems have appropriate filters to ensure equipment runs properly, preventing equipment failure & unscheduled production down time..
Efficient Magnetic filters now offer a huge advantage in increasing the performance of Filtration units and Filter systems / fluid conditioning, and play the major part in improving/reducing system running cost and increasing availability, by effectively and efficiently removing Ferrous contamination, Iron oxide, rust & Magnetite from critical systems, down to sub micron levels, e.g.
Ironbridge Power Station
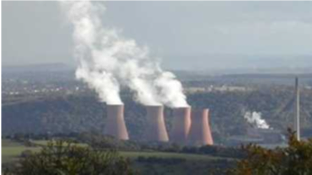
Ironbridge Power Station in Shropshire, UK uses Magnom units to clean general service water to the main heat exchangers, and this has helped them to avoid regular and expensive critical equipment failures.
The power station burns coal imported from Russia, but has plans to switch to burning of wood pellets, to further extend the plants operation.
Operators EON are keen to keep equipment and the plant running ongoing, and have chosen Magnom technology to facilitate this, reducing failure risk & expense and increase power gen availability.
Magnom in Cooling Systems in …
Temelin Nuclear power station in the Czech, Reducing system failures,
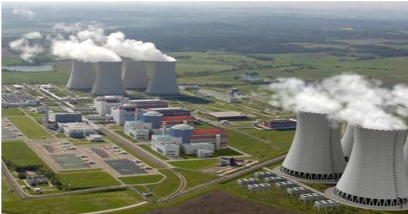
Stainless-Steel Magnom water system products have improved system reliability in a Westinghouse managed nuclear power station in the Czech Republic.
The unit was introduced to reduce the failure of various mechanical devices such as motorized valves in the steam lines, thought previously impossible.
The MagnomTM technology has been installed in the Steam Generator Blow Down sample line at steam generator number 4 – Temelin Nuclear Power Plant.
The parameters of the system water flow in this application line are:
Flow: 12 to 20 l/min
Flow Temperature: About 100 deg. C
Flow Pressure: 6.4 to 6.8 Mpa
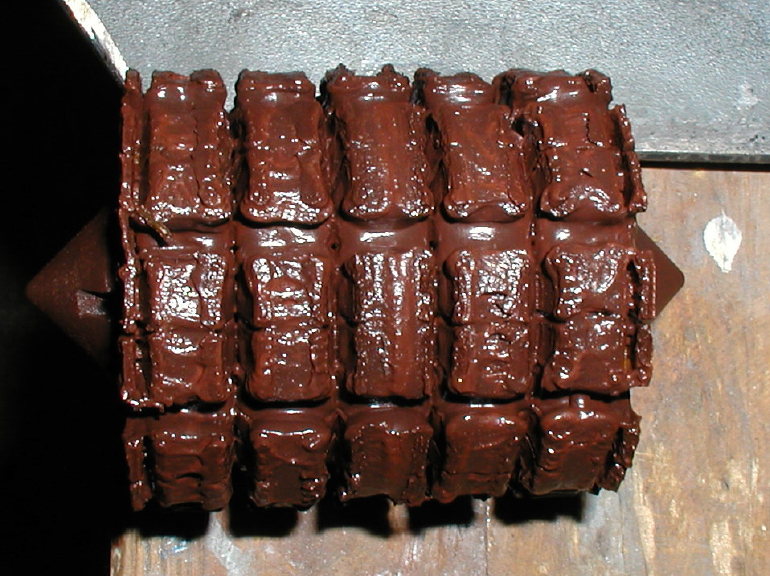
The core in the image demonstrates clearly that the MagnomTM has removed a large quantity of debris from this critical system,
Prior to the installation of the MagnomTM , this debris would have continued to circulate (much of it less than a micron in size) through the conventional filtration used.
This hard and sharp particulate would have/has been been responsible for a chain reaction of wear that causes erosive wear on all valves and static parts of the system, threatening the safety of the entire Nuclear plant.
The engineering manager of this section of the plant believes that the MagnomTM has substantially improved the operation of the specified sample line, this is clearly common sense, in view of the state of the contaminated core above!
General information on this application:
Many power plants have boilers (steam generators) to convert water to steam.
The steam passes through the steam turbine that drives the electrical generator, then is condensed back to water and returned to the steam generator to be converted to steam again. The water has high quality chemistry, but inevitably builds up dissolved solids during the process.
If the level of total dissolved solids (TDS) exceeds the recommended level, sludge and scale can be precipitated in the steam generator. Also water foaming can occur in the steam generator and water can carry over into the process.
To keep the TDS within limits, part of the water is “blown down” (drained) from the steam generator (periodically in some plant, continuously in others) and the water is made-up with high quality water.
It’s an area of great interest to power plant owners and operators on the grounds of efficiency (energy is wasted by the blow down process, but the steam generator then operates more efficiently) and safety (particularly in nuclear plants, where the whole steam generation process is strictly controlled)