Efficient Magnetic filters now offer a huge advantage in increasing the performance of hydraulic systems and their Filtration units and Filter systems / fluid conditioning, and play the major part in improving/reducing system running cost and increasing reliability and importantly availability, by effectively and efficiently removing Ferrous contamination, Iron oxide, from critical systems, down to sub micron levels, e.g.
Protecting transmissions
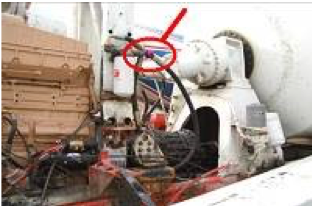
Having spent $8,000 on the rebuild of a 740 HT Allison transmission, American Concrete engineers decided to protect their investment with Magnom filtration, and so avoid ongoing repair and replacement costs, and the lost revenue that would result from future breakdowns.
Taking the advice of an Allison rebuild specialist with 35 years experience, they chose the Magnom in-line Midi filter.
Crane Swing Motor
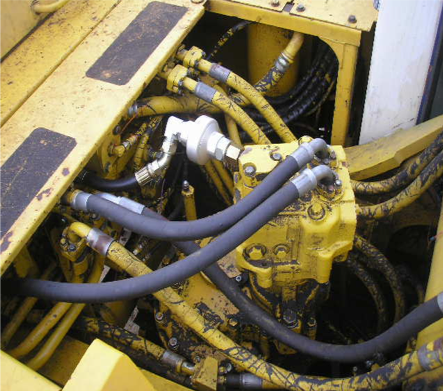
This hard working crane system was suffering accelerated wear,
due to build up of metal wear contamination left circulating in the system by
its conventional (and limited efficiency) conventional filtration,
The inclusion of the Magnom Max unit in the circuit, ensured that all of the super hard and sharp damaging wear material was systematically removed from the fluids, enabling the crane to work harder for longer, without the risk of premature catastrophic failure due to the build up of debris left in circulation.
Caterpillar CAT D11 Dozer… Fan Drive life extension…
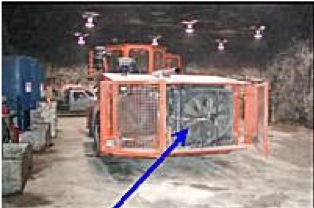
Test Parameters
MAGNOM In-line Midi installed on Caterpillar D8 Hydraulic circuits.
Test Duration was 6 months in the field
Goal of the test was to determine the suitability of the MAGNOM units in the severe environment and the efficiency of the core technology to remove small ferrous contaminants
The In-line Midi units were installed on the D8 hydraulic circuit, downstream of the 10 micron rated spin-on filter
Test Results –
The Midi unit was installed in-line, and remained firmly attached and undamaged during field operations.
In both applications, ferrous contamination was found on the core in visible amounts*.
These contaminants were small enough to pass right through the 10 micron rated barrier filters Remember… This was caught AFTER the conventional filter.
Individual pieces of ferrous metal below 5 microns are invisible to the naked eye.
What was visible during the initial inspection were collected pieces that had formed larger ‘structures’ made up of many smaller pieces.
Test Summary
MAGNOM units, installed on the hydraulic systems, mounted after the traditional barrier filters enhanced the total system efficiency by removing the smallest and most dangerous contaminants.
Eliminating these damaging shards of ferrous metal will extend critical component life, and reduce the risk of catastrophic system failures?
This had the effect of increasing the life of the hydraulic components (Fan Drive in particular) by as much as 5 Times life, with a cost benefit running into the the $15000 plus per vehicle.
Fletcher Construction Equipment
Having already ordered a Magnom Midi In-Line filter for an older machine used in its underground operations, Martin Marietta engineers were quick to realise that it would also be the solution for a brand new Fletcher roof bolter that had gone down very early in its service life.
Given its working environment, it was no surprise to find that the problem was due to contamination of hydraulic valves and our dealer was quick to supply another Magnom filter, which resolved the problems.