Efficient Magnetic filters now offer a huge advantage in increasing the performance of Filtration units and Filter systems / fluid conditioning, and play the major part in improving/reducing system running cost and increasing availability, by effectively and efficiently removing Ferrous contamination, Iron oxide, from critical processes and systems, to sub micron levels, e.g.
Mercedes AMG F1
Magnom magnetic Filtration in Mercedes F1 Engine Production
Nissan Motor Company
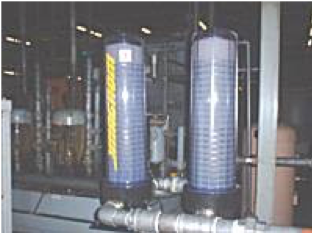
Nissan Motor Company was experiencing regular failures of the lubricant recirculation pumps on grinding machines at their UK crankshaft production shop. Each failure resulted in direct costs of c £1000 and un-calculated costs associated with machine downtime.
The solution provided by Magnom distributor Linden Group was to install 2 Magnom Clear 20 Units in parallel, as polishing filtration.
These were immediately capturing in excess of 8kg of (sub micron) particulate/contaminant every 2 to 3 days, delivering savings in overhaul and downtime costs as well as improved product quality.
Since this installation, Nissan have installed several Magnom Units across the plant, and have now installed the large Magnom MPU product to clean main line coolant systems ‘full flow’ delivering the benefits to multiple machine tools.
BMW Engine Plant
The BMW engine production facility at Hams Hall UK, was the first BMW engine plant to be built outside Germany and Austria, and since 2001 has played a crucial role in BMW Group’s international production network producing four-cylinder petrol engines for both BMW and MINI.
The plant needed to circulate 12000 litres of cooling fluid per day in a centralised system for 8 multi-headed spindle gun drilling machines used in crank shaft production. A Magnom Inline Process Unit, installed offline in dialysis mode, reduced failures and extended coolant life by over 200%.
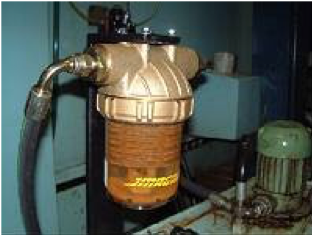
GKN Hardy Spicer, a UK axle manufacturer, was experiencing repeated bearing failures in Nova high frequency grinder machines.
Magnom quickly realised that the bearings in the system were failing through overheating because the cooling jackets around the spindles were blocking with metal debris and rust from the steel parts of the system.
Magnom Clear 5 units were fitted In-Line with the cooling water loops on all of all 64 high frequency spindles to overcome this problem with 100% success . The debris collected proved indeed to be predominantly rust particles, ranging in size from less than 1 micron up to 900 microns.
Realising a significant reduction in production down time, a previously unheard of increase in tool and spindle life, resulting in lower maintenance costs.