… BY ELIMINATING “THE” MAJOR SYSTEM THREAT!
Prevent Hydraulic failure in pumps, motors, valves,
‘fix the cause’!
We must Design & produce the system needed for the job, NOT one over scaled to cope with the attrition caused by exposure to ‘life long aggressive contamination’.
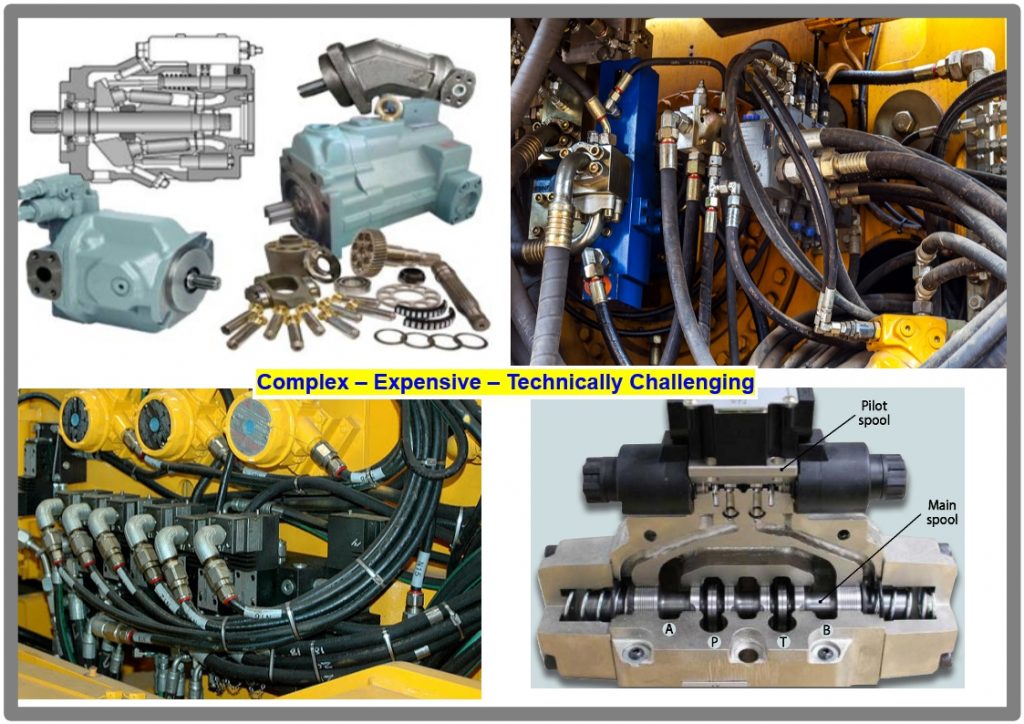
Hydraulic systems are often oversized, as a result of over engineering to try improve reliability and longevity, which typically ends up with poor cost-effectiveness and lower energy efficiency.
In an attempt to reduce the attrition and negative impact caused by compromised conventional & ineffective element filtration, unable to remove Super Hard, Super Sharp, Microfine Metallic Debris left in continuous re-circulation in our hydraulic and lubrication systems.
Remember… “Fluid Systems Would Not be universally fitted With ‘Magnetic Sump Plugs’, if ‘Conventional Filtration’ was doing the Job”
“Just a half hearted attempt at resolving an age old issue?”
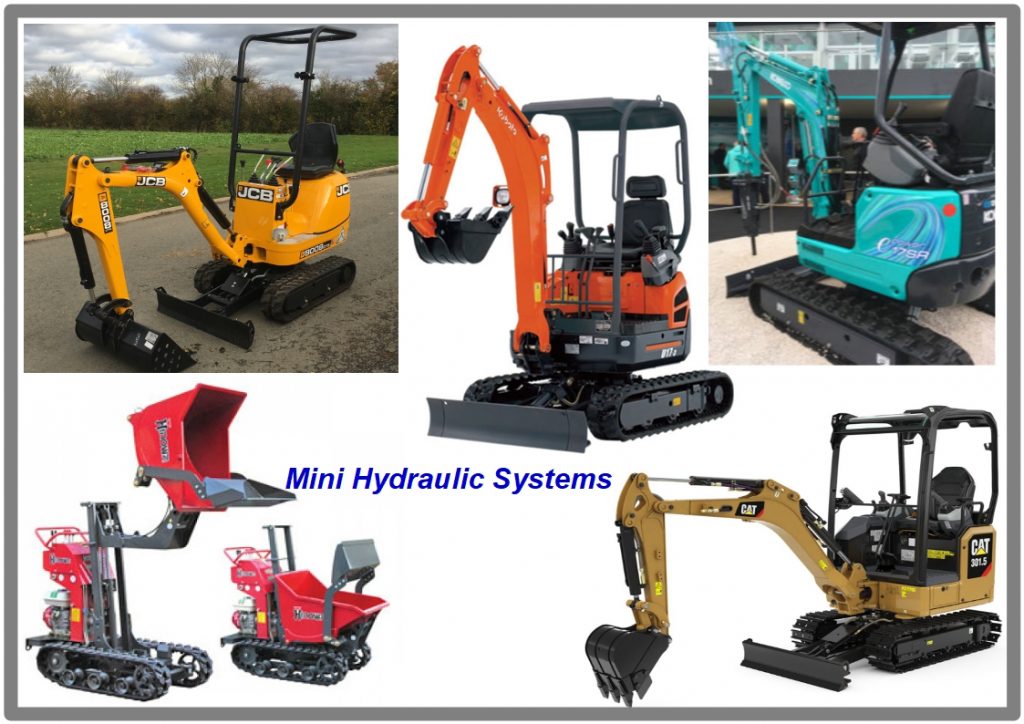
Mini & Micro Hydraulic systems, need to be a small and efficient as is possible, while mainlining reliability and performance in rough service conditions, and can often be used in the hands of relatively untrained operatives,
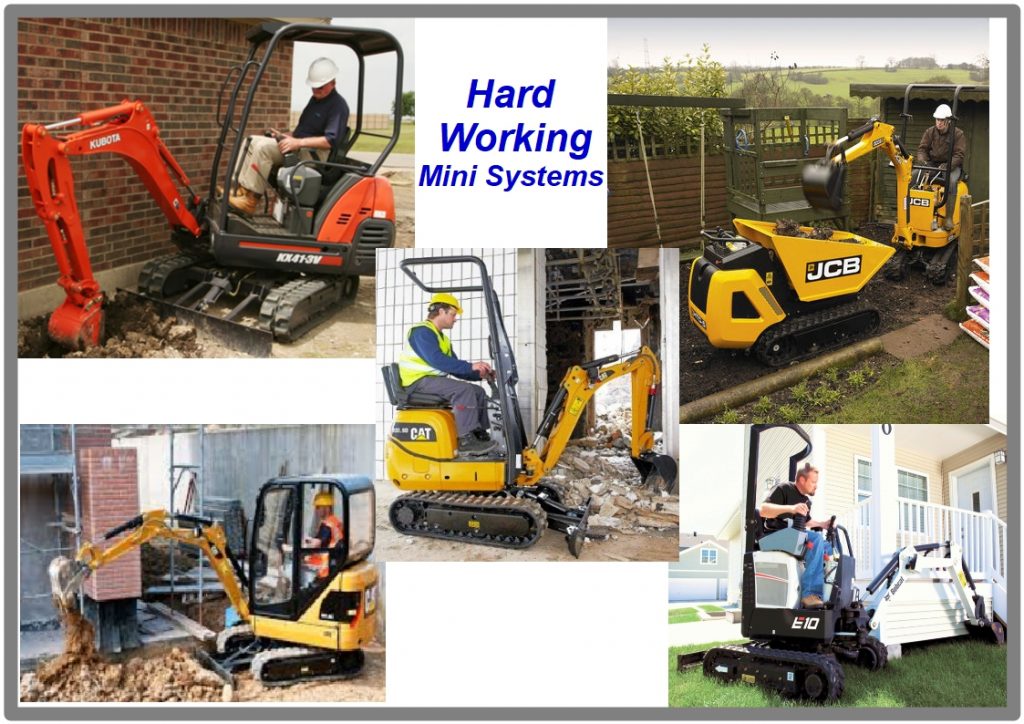
So, system cleanliness & protection from aggressive contamination is just as important as in our larger fluid power systems, and perhaps even more apparent.
In today’s eco-conscious and globally competitive economic environment, we need to endeavour to optimise our designs, to meet the needs of our customers and end users.
A transition to systems in which power is precisely modulated to the requirements of specific tasks within highly complex hydraulic systems is essential.
However, this is frequently compromised as a direct result of historic experience learned from Pump, Motor, Valve & Actuator premature failures, that can be attributed to aggressive contamination, left in circulation within systems by compromised barrier filtration products.
UNTIL NOW!
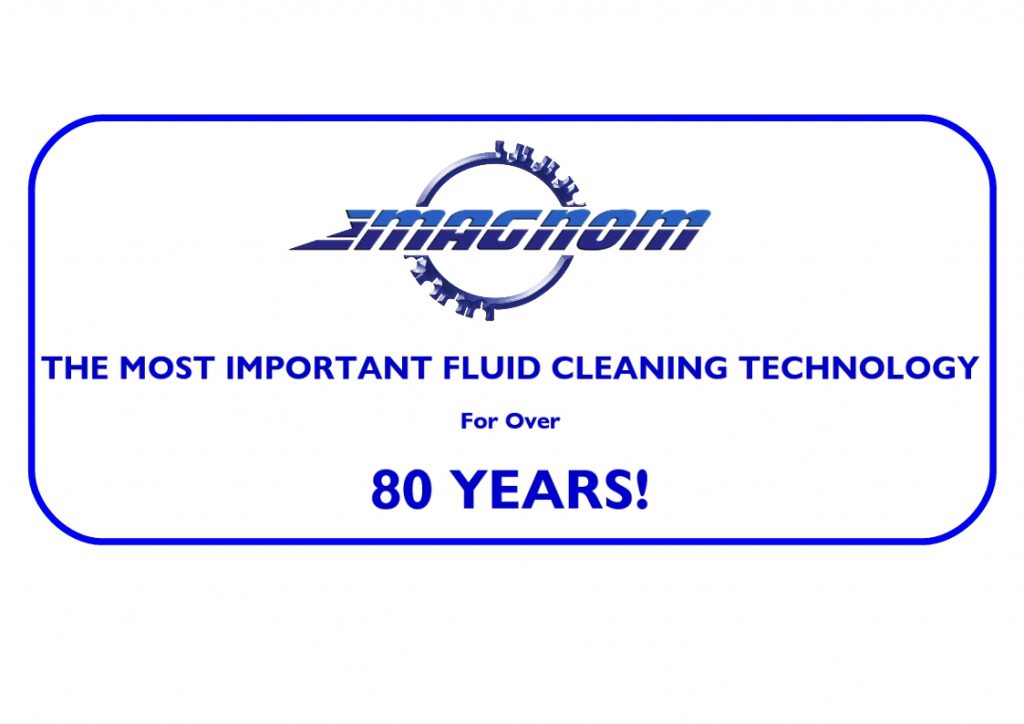
Learn how Magnom Products can enhance and optimise your system designs to better meet the application requirements, to help create an innovative energy-saving approach to your hydraulic system design.
