MAGNOM & CORE!
The patented magnetic filtration solution for ALL fluid systems
Magnom & Philadelphia Gear (Timken Power Systems) join forces to eliminate transmission / gearbox failures
Magnom MAX XL product line, now forms the backbone of Philadelphia Gear’s CORE system,
Which virtually eliminates ferrous metal contamination as a cause of lubrication related failures in gearboxes.
With more than a century of gear design and manufacturing behind them Philadelphia Gear understands how lubricant contamination can negatively impact the operation Of critical rotating equipment. This is why we are proud to announce the arrival of a breakthrough technology that, quite simply, makes this problem a thing of the past.
The solution is CORE — ‘Continuous Oil Rescue Equipment’
We all face the same challenges:
How do we increase operating efficiency while eliminating unplanned downtime?
How do we extend the life of our equipment? How do we postpone the wear out phase of the infamous bathtub curve?
Part of the answer to that question lies in the degree to which gearbox lubricants are kept free of ferrous
metal contamination.
That’s where the Philadelphia Gear and the CORE System comes in.
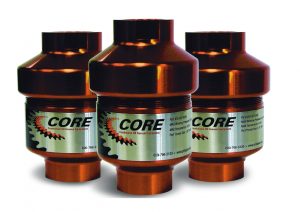
Heres why:
The smallest particle that can be seen by the human eye is 40 microns. But ferrous metal particles much smaller than this can cause extraordinary amounts of damage to rotating equipment over time, That is why upgrading your
existing filtration system to include CORE is so important. CORE tan remove particles as small as one micron or, put another way, particles as small as one millionth of a meter.
Machine casualties (Often referred to as machine infant mortality) tend to occur during the break-in period Of operation on the typical bathtub curve, After that the machine settles into its normal operation mode and tends to run
well as long as it gets adequate levels Of preventive maintenance. Then, at some point in time, the machine inevitably enters its wear Out phase.
In many applications an interesting phenomenon has been taking place through all Of this time. Ferrous metal wear particles have been floating through the lubrication system and taking a gradual toll on rotating elements within the gearbox. Bearings, gears, pinions, etc., are all susceptible to varying degrees of damage over the life-cycle of the equipment due to this type Of ferrous metal contamination.
The CORE system is designed to trap these particles from the moment the filter is installed and oil begins to pass through it and, by doing so, CORE can literally move the wear out line further along the bathtub curve and extend
The Evolution of Metal Filtration Technology
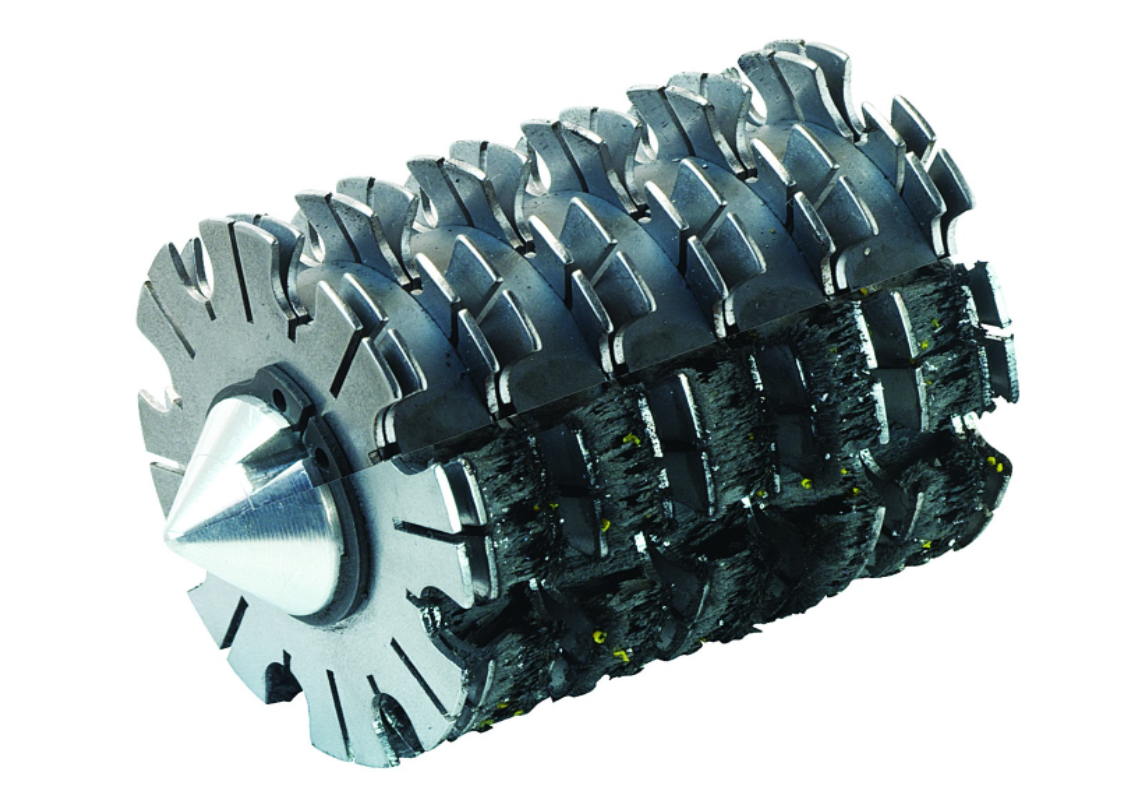
An engineer working on performance transmissions and engines for racing vehicles found that contamination of the lubricant was Causing a reduction in performance and. eventually, catastrophic failure. Traditional barrier filtration techniques resulted in pressure drops that inhibited the fluid flow, which made them unusable in high-speed or critical applications. It is an age-old problem that defines tribology, the science of the mechanisms of friction. lubrication, and wear of interacting surfaces that are in relative motion.
The engineer wasn’t satisfied with a traditional approach to solving this problem. After all, the problem had been around as long as gearboxes themselves and was considered an inevitable maintenance issue. Then, after years of experimentation, a breakthrough occurred.
By using a system comprised of a series of annular magnets shrouded by steel plates, it was discovered that oil would pass through the flow channels at the magnets’ outer edge. While harmful contaminants were simultaneously stripped out and deposited in the collection zones that resulted from the strong magnetic fields surrounding the oil
This technological breakthrough has been proven season after season within the demanding Formula One racing environment and is now routinely specified on new race car designs. And now, Philadelphia Gear is bringing its own branded solution of this patented technology to the industrial marketplace.
Critical equipment is critical equipment and it doesn’t have to be roaring around a track at 200 MPH to earn that designation. Whether it’s a coal crushing application in a power plant, a conveyor drive in an automotive plant or a pump drive at a remote pipeline installation, CORE technology gives you the peace of mind that comes with knowing your lubricant is being kept as clean as possible.
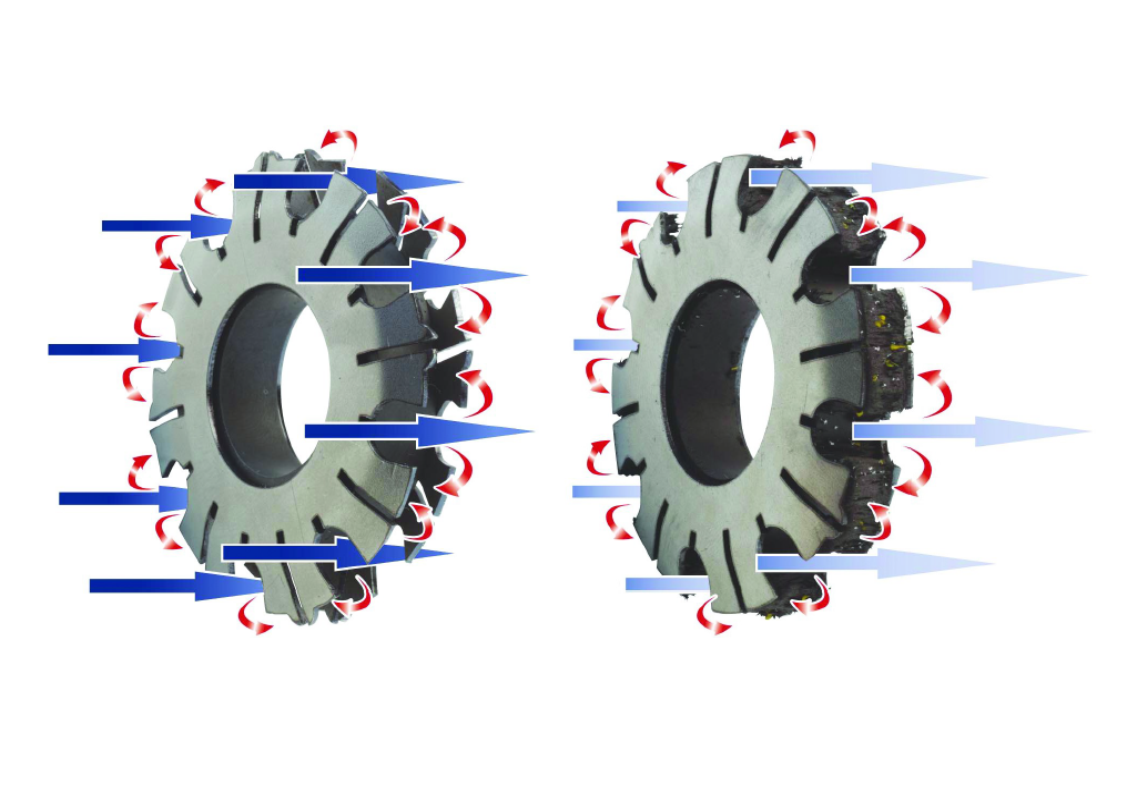
At the centre of the Continuous Oil Rescue Equipment is a series of annular magnets with larger steel plates shrouding them. These plates, which have a series of flow channels running through them, become fully magnetised. When the oil is filtered through these plates, it is subjected to a high magnetic flux gradient, caused by the focusing of the magnetic field at the tips of the plates.
The result is that any contaminant is drawn into collection areas (out of the oil flow) between the plates.
The adjacent diagram shows how oil (blue arrows) passes through the wide flow channels at the edges of the steel plates and exactly how contaminants are removed by the magnetic field (red arrows) for storage in the collection zones. It’s important to note that this occurs with virtually no pressure drop even when the CORE is fully loaded with contaminant.
The reason the filter does not create a pressure drop is because CORE was designed such that the flow channels sum to a greater flow volume than that of the inlet pipe. Therefore, as the contaminant is drawn into the collection zones by more efficiently focusing the magnetic flux, refraction of the oil compacts the contaminant and ensures that it is held out of the flow paths. This results in a negligible pressure drop, While at the same time, also helps prevent “wash off’ since – unlike magnetic sump plugs, for example — the contaminant is isolated and can not wash back into the oil.
Benefits of Near Zero pressure Drop
- • For the first time fine filtration Can occur on the Suction side of the pump
- • CORE is more accessible for condition monitoring of the power transmission system
- • Pressure drop is avoided even When the filter element is
- • Oil viscosity does not effect the filters performance.
- • Because the magnetic filter element has an area equal to 110% of the inlet, there is zero risk of oil pressure drop in- side the gearbox upon installation.
Additionally, because CORE holds significantly more contaminant than a conventional filter – as much as 2 lbs of ferrous metal contaminant between cleaning/servicing – it can operate for long periods without service. When service is needed the unit can be easily cleaned and immediately put back to work.
Summary Of Metal Filtration Benefits
• Reduced failure rate of power transmission equipment
• Lubricant life extended of wear particles ore removed
• Reduction or elimination of spare filter inventory
• Cleaner Oil means cooler and lower operating temperatures
• Equipment life extended as wear particles are removed
• No significant pressure drop as lubricant Is pumped through filter
• Filters can be cleaned and immediately put back in service
• No pressure drop means filters can be installed upstream of the pump
• Protection Of the pump With minimal risk Of cavitation
• Cost effective insurance to maximise equipment available time
Most Frequently Asked Questions About CORE
HOW Long Will A CORE Unit Last?
The magnets inside your CORE unit have a half-life of at least 5O years. The housing is made of high grade 6082 aluminium so, for all intents and purposes, each CORE unit is designed to outlive virtually any machine.
What Size Lube Lines DO I Need to Install A CORE System?
There are two versions of CORE. The larger unit is designed for lube pipes that range between I ,25″ – 2.0′ in diameter. and the smaller unit is designed for piping between 0.5” – 1.25″ in diameter.
How Do I Clean The CORE After Installation?
Each unit comes with a set of instructions on cleaning, but in general the most effective way is to simple open the unit and then use an 80 PSI air line and blow off gun/nozzle to clean the magnetic core of debris trapped in the collection zones. In this manner the CORE can be efficiently and effectively cleaned and readied for re-installation and reuse.
How Will I Know When the CORE is Full?
Disconnect the CORE unit from the lube system and remove the flanged or threaded cover. We recommend this be done annually during the unit’s routine cleaning cycle. Those customers with highly contaminated lube systems may choose to do this more frequently.
HOW Much Debris Does A CORE Unit Hold?
The large unit holds up to two pounds of debris and the small unit holds nearly one pound of debris.
What if I Don’t Want to Shutdown my process to perform Maintenance on CORE?
CORE can be configured in a duplex arrangement that makes unit shutdown for maintenance unnecessary. The units can also be piped in a “kidney loop” configuration to allow them to be valued off for cleaning If a duplex arrangement is not feasible for whatever reason.
What is the physical Size of A CORE Unit?
The CORE is designed to be compact The large unit is 8″ in diameter and 9.5″ long at widest and longest points, respectively. The smaller unit is S” in diameter and 6.5″ long.
How Much Does A CORE unit weigh?
The large unit weighs approximately 10 lbs. and the smaller unit weighs approximately 5 lbs.
What Does the CORE System Cost?
There are several variables that impact the cost of the CORE system including how many units are being sold, are they in a single or duplex configuration and, most importantly, Which size CORE is necessary to fit your application.
Please ask for price details, the units are not as expensive as many conventional filters, But the pay back on purchase cost can be weeks to months.
The costs of downtime, the cost of CORE is negligible and has been priced to be a “no-brainer” addition to even the tightest maintenance budgets.
For:- Price, availability, and technical assistance, please contact :-
Or